How to Build 3D Printing Prototypes in the Automotive Industry?
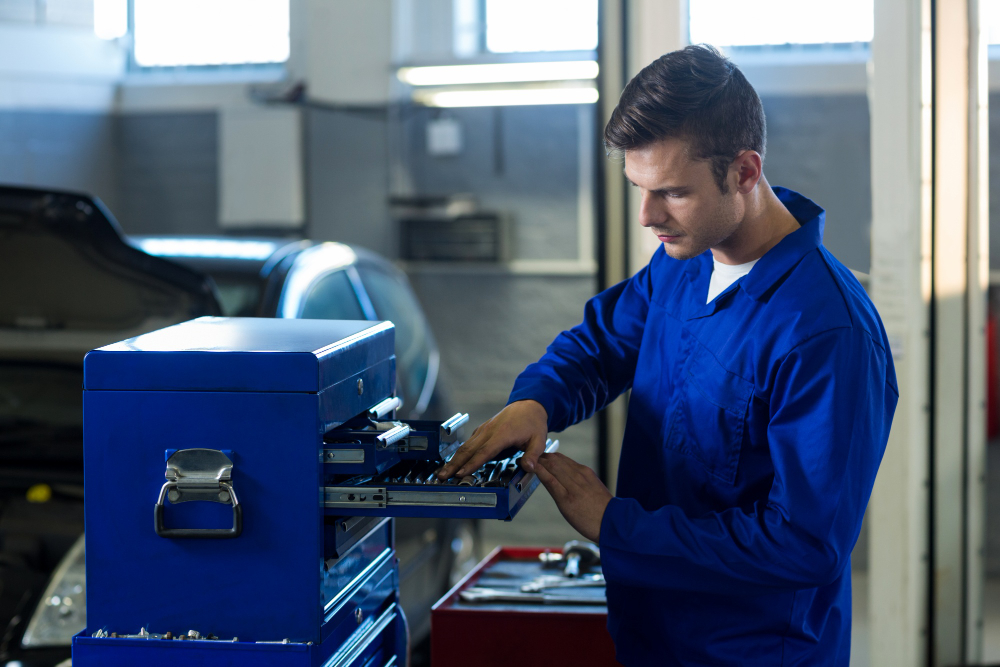
The future is now: the automotive industry has always been committed to innovation and continually revolutionizing both products and processes. It continues to lead with its use of rapid prototyping and 3D printing.
Known for its groundbreaking development in the use of assembly lines in the early 1900s, the automotive industry has always been at the forefront of creating change. Processes like assembly lines and lean manufacturing best practices, first adopted by automotive titans, have been translated into many other manufacturing uses.
More recently, CAD design and 3D printing have once again shaken the landscape and allowed rapid prototyping to become a key feature of the automotive industry. It enables both creativity and speed, as engineers are able to iterate quickly and test ideas nearly immediately.
Traditional machining removes material, using equipment like milling machines, lathes, and drill presses. A sharp cutting tool removes material from an existing piece of metal till the desired shape is created. On the other hand, a 3D printer creates objects one layer at a time using commands from a digital file, till it is built into the desired shape. This way of starting from nothing and adding material is why it is also known as additive manufacturing.
3D printing is a far faster process than traditional machining, since it is much more adaptable to change and iterations. This is why it is so valuable in the design phase for automotive parts. For example, if an automotive engineer wants to test a new shape of cup holder, they can design it in CAD and have it ready to test in as little as 24 hours. Once complete, they may decide the design isn't quite how they wanted it and so they make changes and do it again. Within a few days, they could have a design that would have taken weeks or even months to complete using traditional manufacturing methods.
These are some reasons why automotive manufacturers are turning to 3D printing:
Speed and agility: As mentioned above, traditional prototyping can be a very time-consuming endeavor. 3D printing allows users to test, make changes, and test again very quickly.
Cost savings: Partly because it’s so time-consuming, traditional manufacturing is typically more expensive than 3D printing. At the prototyping stage especially, parts can be created at a fraction of the price of traditionally made products.
Design freedom: 3D printing allows for much more flexibility in design. Here’s a quick example of why that is: a drill press can only create a straight hole inside a solid object. On the other hand, as a 3D printer puts down one layer of material at a time, it can create any number of tubes, curves, bends or complex shapes inside what ends up looking like a solid object.
Customization: 3D printing allows parts to be customized for specific clients. Although this is often thought of as strictly for aesthetics or luxury, it can also be used in security devices. For example, Ford has used 3D printing to customize their lug nuts in a way that only the car owner can allow the wheels to be removed.
3D printing is not new for major players in the automotive sector. Companies like Ford, BMW, Koenigsegg, and Lamborghini have long since adopted this technology to design and create parts quickly.
Making the transition to 3D printing is more than just using different tools and equipment though. It is a different mindset to design for your needs and desires, versus designing based on traditional machine tool processes. The best automotive businesses will continue to set themselves to understand its capabilities, integrate it into their workflows, and really learn to leverage its potential.
Learn more about 3DPrinterOS - the most trusted 3D printing management software for Higher Education, Enterprises and OEMs. Fill out this form to get in touch with our experts.
Manage the workflow and permissions for your users
Share files and 3D printers to groups of users
Control your 3D printer fleet through a browser
Cloud slicer and toolpath viewer
Book your personalized assessment now and get your free trial.