What is the best flexible filament for my 3D printing needs? – My3DMatter study
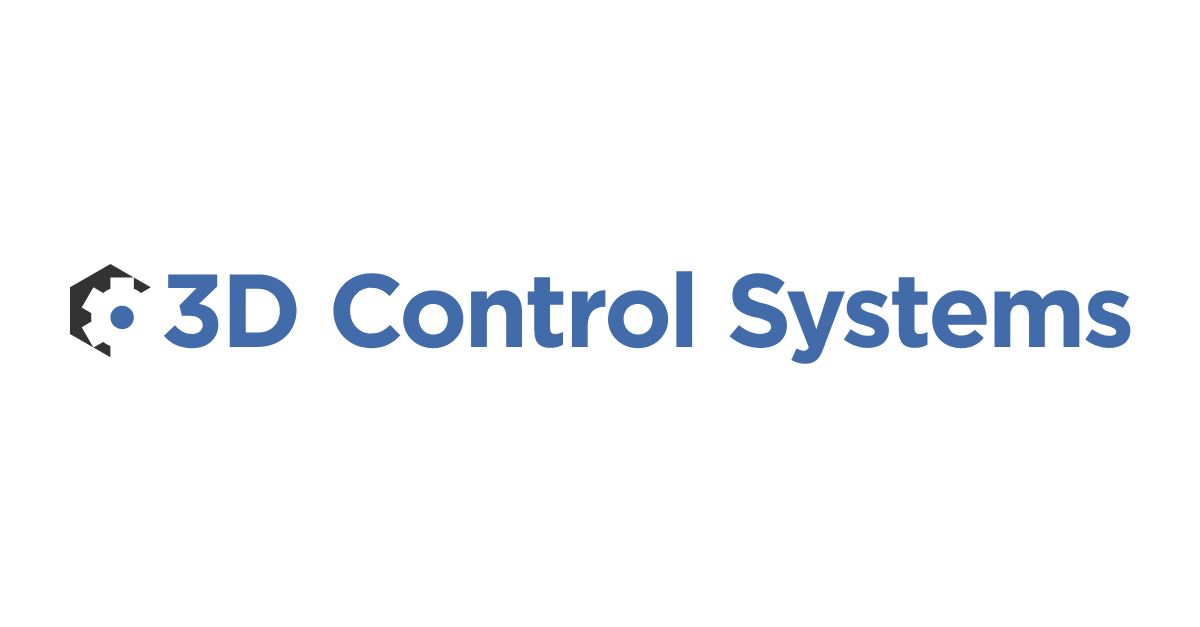
Flexible filaments arrived on the market a couple of years ago and have really broadened the range of objects that can be made with personal 3D printers. While flexibility is a new dimension to the material selection that users can now tap into, this dimension has not been well investigated.
There are many suppliers of flexible materials, and this diverse product selection is also associated with a wide range of filament flexibility levels, mechanical performance, visual quality and processability. Also, there is currently little understanding of how to use a given filament to get the right flexibility for prints, in particular by adjusting the infill %.
This study compares a set of six flexible filaments along various criteria to provide users with a point of comparison among current suppliers. It also gives insight into how to use flexible filaments to reach the right level of flexibility, and the key parameters to adjust when printing this type of material.
Choosing the right flexible filament is first and foremost linked to how flexible the user wants his object to be. So in all our results tables, we listed the products by order of flexibility: SemiFlex is the least flexible filament and FilaFlex is the most flexible.
Here are the high-level results from our study[1]:
Overall, the quality of the filament selection is very good. Making flexible filaments is not easy so there is a natural filter on manufacturers who are able to do it. In addition, only companies that are confident in their materials have taken part in the study[2], so there is also a selection bias in this sample.
The study shows that filaments that are more flexible tend to have lower quality and process grades, due to their physical nature. 3D printers were designed for rigid filament, and the adaptation to flexible filaments decreases the visual quality and printability of objects.
NinjaFlex proposes two great filaments with different levels of flexibility: SemiFlex and NinjaFlex. They are a bit more expensive than the competition, but their overall assessment seems to justify some premium, at least in the case of SemiFlex.
Polymaker’s PolyFlex is also a very good semi-flexible filament, very easy to print and with great visual quality, but does not match the mechanical performance of the rest of the selection. However, its lower price makes for a great option.
MadeSolid’s FlexSolid has good mechanical performance but is visually not on par with SemiFlex and PolyFlex.
Oo-kuma’s TrueFlex is also a great flexible filament as it is the only one in the flexible category to have good strength. It is also the cheapest of the selection, which makes it an attractive option.
Very flexible filament FilaFlex is hard to print, and does not have a good visual quality, so it should be reserved for applications where higher flexibility is crucial and NinjaFlex or TrueFlex are not flexible enough.
Before we get into the testing analysis, it is important to understand what flexible filaments are and what purpose they can be used for.
A flexible material is one that can be deformed significantly under a load and revert back to its initial shape when the load is lifted.
The filaments selected in this study are Thermoplastic Elastomers, most likely of the Thermoplastic Polyurethane chemistry (TPU)[3]. This is a family of plastics that can be melted and shaped via the FDM process, but have characteristics close to rubber. Rubber itself cannot be used for FDM, because it is a thermoset and therefore cannot be melted.
For the study, we needed to find a metric to quantify “flexibility”. So we are using a filament’s hardness (opposite = softness) as a proxy for flexibility as hardness is closely correlated to stiffness (opposite = flexibility). A material’s hardness is measured on a “Shore hardness scale”. There are several Shore hardness scales depending on the hardness of the object, but for the range of materials we have here, the Shore A scale is most appropriate[4]. This scale goes from 0 to 100 and below are a few objects placed on the scale for reference:
We then divided the filaments into two broad categories: semi-flexible and flexible. While they are all “flexible” in the sense that there are more flexible than other filaments offered on the market, the range of flexibility of the filaments is still broad so we chose to split them into two groups.
At 100% infill, the filaments we are studying have the following hardness:
Shore HardnessFilamentsSemi-flexible90-93ASemiFlex, PolyFlex, FlexSolidFlexible74-85ATrueFlex, NinjaFlex, FilaFlex
While this range does not cover the whole Shore A hardness scale described above, by reducing the infill the printed object can have a much lower hardness than the 100% material. 3D Matter wanted to quantify the hardness that can be reached by adjusting the infill %, so we printed a range of specimens[5] with varying infill % and measured their hardness with a durometer, while keeping other parameters constant:
Here are the results:
This scale will help users adjust infill % to get to the required hardness. For example, if the hardness required is that of a tire tread (60A), the user can try printing a flexible filament at 50% infill, or a semi-flexible filament at 20% infill.
Users need to be careful however: same hardness does not mean that other mechanical properties are the same as well. For example, printing a flexible filament at 70% infill does not “reproduce” a semi-flexible filament printed at 30% infill: while their hardness levels are very close (~70A), the weight, max stress and elongation at break are still very different.
Here are the key evaluation criteria for the performance, quality and process tests:
The tests were carried out while controlling for all environmental parameters, all filaments from the same material being printed on the same printer with the same settings:
The testing procedure in this study was modified from that of our previous studies (PLAand Improved filaments) as it was adapted to achieve the most appropriate analysis for flexible filaments:
A flexible filament shows good performance when it has a high strength, a high elongation at break and a good elasticity (a.k.a. resilience).
To test these criteria, we performed a tensile test on 3 specimens of each filament, a hysteresis test on 3 specimens, and 5 hardness tests on 1 specimen of each filament to get the following values:
The tensile and hysteresis tests were carried out with a universal testing machine, at the PIMM lab of the Ecole Nationale Supérieure des Arts et Métiers ParisTech. The hardness test was conducted with a Shore A durometer. The data was compiled and averaged to build the following table (note: the “low / medium / high” characterization used here is relative within this filament selection and does not represent an absolute assessment):
In line with our intuition, semi-flexible filaments show a higher strength, lower elongation at break and lower elasticity than flexible filaments.
Within the semi-flexible category, SemiFlex and FlexSolid show very similar performance, with the highest strength and good elasticity.
Within the flexible category, NinjaFlex and Oo-kuma’s TrueFlex have very good mechanical performance:
FilaFlex is very soft and also shows very good performance, but actually have a slightly lower elongation than NinjaFlex, and have lower strength.
In September 2015, we released our new quality testing file: Testman. We first did a few trials to find the best extrusion temperature for each filament. We printed two Testmans and one “owl” (.stl file from Thingiverse) under the best conditions for each filament. Then three people were asked to rank each batch from “best looking” to “worse looking”, and also group them by quality categories, along the list of criteria described here.
Based on this testing procedure, the following conclusions were drawn:
In absolute terms, current flexible filaments on the market do not show very good visual quality. Even the top flexible filaments in this list still have a visual aspect that is lacking that of rigid filaments.
However, within the selection, there are also significant differences. While more flexible filaments tend to show poorer visual quality, it is not a systematic correlation.
PolyFlex and SemiFlex come out on top pretty clearly, both in terms of the quality of the details and texture, and on the geometrical accuracy.
TrueFlex and NinjaFlex follow in aggregate assessment, but TrueFlex is better on shapes and geometry, while NinjaFlex has a better general aspect.
The other filaments have a worse visual quality, and are not advised for intricate detail work.
Flexible filaments are inherently harder to print than rigid filaments, mainly because the mechanical setup of FDM 3D printers is designed for the latter. Flexible filaments become more easily tangled into the extruder, have a harder time being pushed and pulled by the motors, and cannot retract as well as rigid ones.
The key parameter to adjust when printing flexible filament is to reduce the printing speed, and this was one of the extra tests we conducted to characterize the filament’s processability. We increased speed for each filament until the print was not acceptable anymore (e.g. gaps appeared, or the flow of material stopped), and that gave us the “maximum printing speed”.
Other criteria we used are the same as our usual procedure: we gave a better grade if the spool is convenient to use (right dimensions, easy-tie for the filament… etc.), if it is easy to feed into the printer, if the filament is not getting tangled, if the filament sticks well to the platform, and if there is no or limited post-processing needed.
There is a clear correlation between filaments’ flexibility and their processability: the more flexible, the harder to print. This is true in particular with regard to the maximum printing speed reached. Semi-flexible filaments can be printed up to 80-90mm/s, but flexible filaments can only reach 30-65mm/s.
While printing speed is an issue with flexible filaments, build plate adhesion generally is not. They seem to adhere very well to the platform (glass or blue-taped), even without a heated bed or other change on the surface.
Another issue faced by the user is that the amount of material coming out of the printer is sometimes lower than expected: a certain infill is computed, but what comes out can in fact be much lower. This can be corrected, for example by applying an extrusion multiplier or extruding at a higher temperature but it is not convenient.
Flexible filaments are a great addition to the range of materials available for personal FDM printers, especially for the new mechanical properties they offer. Their printability and the objects’ visual quality are not as good as rigid filaments, so their initial use may be for objects where complexity is not as high. Hopefully, advances in the hardware/material coupling will increase their ease of use and accuracy in the next few years.
Users can also start using the possibility to adjust infill with flexible material within a single print. New softwares now enable printer users to localize infill to make some parts of a given object more flexible than others, giving it functionalities that mimic a multi-material object. By further investigating flexible material, new applications for 3D printing could be developed.
We do not pretend to have an exhaustive test. In particular, the test does not account for the following parameters:
To learn more about My3DMatter and their filament studies please visit their website here: http://my3dmatter.com/
[1] The grades given in this study do not take into account how flexible the material is. Rather it is an evaluation of the quality of the filament for a given level of flexibility, i.e. we did not give a higher performance grade because a filament was more flexible
[2] Companies that decline our service offering are not included in the study
[3] Note: there are also flexible PLAs or flexible PETs in the market but they are very different in chemistry and performance. Their ability to deform and come back to their initial shape is much lower than the selection studied in this paper, so we chose to leave them out, as they would be very difficult to compare.
[4] For more rigid materials such as PLA and ABS, the Shore D scale is more appropriate.
[5] shape defined in ASTM standard D2240
Learn more about 3DPrinterOS - the most trusted 3D printing management software for Higher Education, Enterprises and OEMs. Fill out this form to get in touch with our experts.
Manage the workflow and permissions for your users
Share files and 3D printers to groups of users
Control your 3D printer fleet through a browser
Cloud slicer and toolpath viewer
Book your personalized assessment now and get your free trial.